Anúncios
Done improperly, it can lead to significant health risks, property damage, and loss of valuable goods. This post is dedicated to unraveling the art of moving heavy containers safely. We delve into key insights, indispensable tips, and practical tricks that will elevate your approach to handling heavy loads, making it efficient, safe, and less strenuous.
Are you in a profession that necessitates dealing with heavy containers? Or perhaps you’re a homeowner preparing for a big move? Regardless of the scenario, this guide will come in handy. It highlights the essentials of weight distribution, proper lifting techniques, and the importance of utilizing the right equipment. By the end of this journey, the daunting task of moving heavy containers will seem like a cakewalk!
Anúncios
Furthermore, in a world where time is money, efficiency cannot be compromised. That’s why we’ll also explore ways to streamline the process of moving heavy containers. Expect to learn about the role of planning, teamwork, and communication in expediting tasks while maintaining safety standards.
Lastly, but importantly, we’ll underscore the significance of injury prevention. Safety is paramount when dealing with heavy loads. By incorporating our tips into your routine, you can minimize the risk of back strains, hand injuries, and other physical harm. So, let’s master the art of moving heavy containers safely together!👷🏽♀️👍🏼
Anúncios
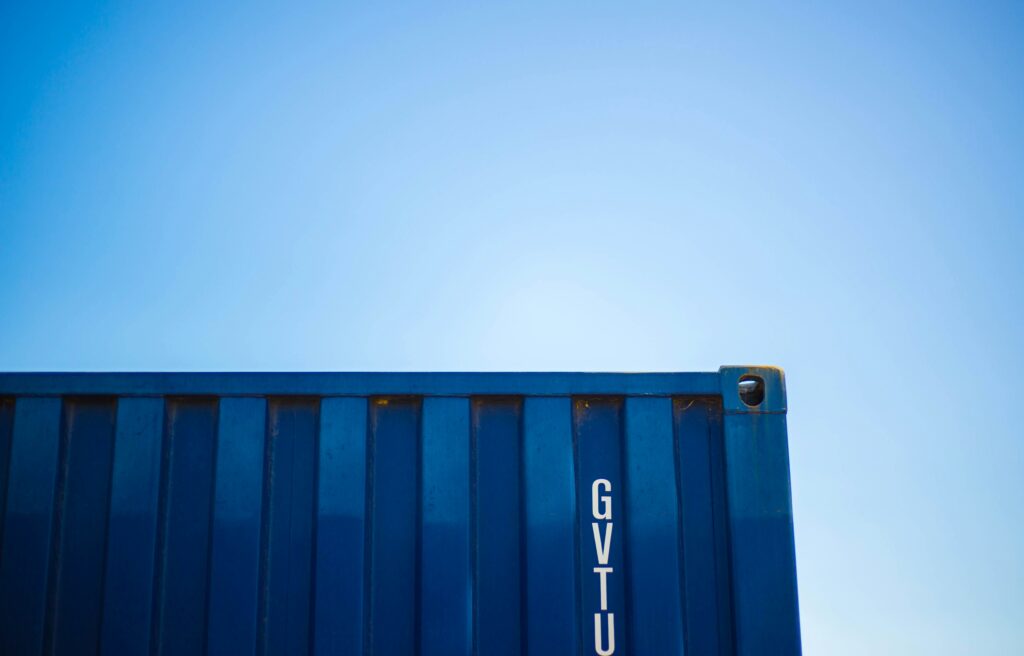
Understanding the Basics: What Are Heavy Containers?
Heavy containers are large, durable units specifically engineered to store, secure, and transport high-weight goods across various industries. Commonly made from steel or reinforced aluminum, these containers are essential components in global supply chains, playing a central role in sectors such as international shipping, construction, logistics, mining, manufacturing, and warehousing.
These containers come in standardized forms—such as ISO intermodal containers, which can be easily transferred between ships, trains, and trucks—or custom-built configurations designed for specialized cargo, such as machinery, raw materials, or hazardous substances. While the container itself may weigh several hundred kilograms when empty, it can exceed 20 tons (40,000+ lbs) when fully loaded, depending on its size and purpose.
Due to their immense weight and bulk, handling heavy containers requires more than just physical power. It demands technical training, mechanical assistance, and a strong emphasis on procedural safety to avoid workplace incidents.
Why Is Safety Important in Handling Heavy Containers?
Dealing with heavy containers is inherently hazardous. Without the proper safety measures in place, routine tasks such as loading, unloading, stacking, or transporting containers can quickly become dangerous. The risks aren’t hypothetical—they are well-documented causes of injury and death across logistics and industrial environments.
Common Hazards Include:
- Crush Injuries: Workers can become pinned between containers, vehicles, or walls if containers shift or are mishandled.
- Falls from Height: Accessing the tops of stacked containers or securing loads can expose workers to dangerous heights.
- Struck-by Incidents: Forklifts, cranes, and container movers can cause injuries when containers swing or fall unexpectedly.
- Equipment Malfunctions: Defective lifting gear, corroded fasteners, or overloading can lead to catastrophic failure during lifting or movement.
The Cost of Unsafe Practices
The consequences of poor safety practices go beyond the physical harm to workers. They can also include:
- Damage to goods or cargo, leading to delays and customer dissatisfaction.
- Destruction of expensive equipment, including forklifts, cranes, and loading docks.
- Operational downtime, which reduces productivity and increases overhead costs.
- Legal liabilities and regulatory fines, especially if workplace safety laws or OSHA standards are violated.
- Reputation damage to the company, making it harder to retain business or attract skilled workers.
Investing in robust safety protocols, employee training, and reliable equipment is not only a legal and ethical responsibility—it’s a strategic necessity. Organizations that prioritize safety typically enjoy lower turnover, fewer interruptions, and higher overall efficiency in container handling operations.
Tips and Tricks for Handling Heavy Containers Safely
Handling heavy containers safely requires a combination of proper training, equipment, and procedures. Here are some key points to consider:
Proper Training
Training is the first and most important step in ensuring safety when handling heavy containers. Workers should be adequately trained in manual handling techniques, as well as the operation of any equipment they will be using.
- Manual Handling: Even though most of the heavy lifting will be done by machinery, workers still need to be trained in manual handling to prevent injuries when loading and unloading goods.
- Equipment Operation: Operating heavy machinery requires specialized training. This includes not only how to operate the machine, but also understanding its limitations and safety features.
Use of Appropriate Equipment
The right equipment can make the difference between a smooth operation and a disastrous one. Different types of equipment are used depending on the weight and size of the container, as well as the specifics of the task at hand.
- Forklifts: These are commonly used to move smaller containers around a warehouse or onto trucks. They are versatile and relatively easy to operate, but they also have their limitations and need to be used correctly to prevent accidents.
- Crane Trucks: For larger, heavier containers, a crane truck may be necessary. Crane trucks have a greater lifting capacity than forklifts and can reach higher, but they also require more skill to operate.
Injury Prevention Strategies
Preventing injuries while handling heavy containers requires a multi-layered safety approach that goes beyond just having the right equipment. While training and mechanical aids are fundamental, integrating organizational safety practices, consistent oversight, and personal responsibility into daily operations is key to minimizing workplace accidents. Below are some critical strategies to reduce injury risk in environments where heavy containers are moved, stored, or transported.
Use of Personal Protective Equipment (PPE)
Personal Protective Equipment (PPE) forms the first line of defense for workers exposed to physical hazards. It acts as a protective barrier against injuries resulting from dropped objects, sharp edges, moving machinery, and environmental risks commonly found in container handling operations.
Essential PPE for Handling Heavy Containers:
- Safety Footwear (Steel Toe Boots):
Protects the feet from crush injuries caused by falling containers or handling equipment. Anti-slip soles are also important in reducing fall risks on wet or oily surfaces. - Gloves:
Durable gloves provide grip and protection from sharp edges, abrasions, and chemical exposure. Choose gloves appropriate for the task—cut-resistant gloves for metal containers, or thermal gloves for cold environments. - Hard Hats:
Protect the head from overhead impact, particularly during stacking, crane operations, or movement of suspended loads. Helmets should meet ANSI/ISEA or EN safety standards depending on your region. - High-Visibility Clothing:
Vital in busy yards or loading areas where workers are in proximity to forklifts, reach stackers, and cranes. Reflective vests or jackets improve visibility during day and night operations.
Additional PPE Based on Environment:
- Safety Harnesses and Lanyards:
Required when working at height, such as securing cargo on tall container stacks or accessing rooftop container units. Must be used in conjunction with approved fall arrest systems. - Hearing Protection:
In environments with constant machinery noise—such as port terminals or industrial yards—earplugs or earmuffs protect against long-term hearing damage. - Eye and Face Protection:
Safety goggles or face shields may be necessary when cutting container seals, grinding, or when there is a risk of dust, debris, or chemicals.
PPE Best Practices:
Training and Compliance: Workers should be trained not only in the proper use and maintenance of PPE, but also in why each item is important for their specific tasks. Compliance should be enforced as part of the organization’s safety culture.
Regular Inspection: Ensure all PPE is inspected before each shift for wear, tear, or damage. Damaged PPE should be replaced immediately.
Proper Fit: Ill-fitting PPE can cause discomfort or reduced protection. All gear should be correctly sized and adjusted to the individual.
Implementing Safety Procedures
Safety procedures are the backbone of any high-risk operation, especially when dealing with heavy containers. These procedures serve as a standardized framework for minimizing hazards and ensuring that every worker, from new recruits to seasoned professionals, understands how to perform their duties safely and efficiently.
What Safety Procedures Should Include:
- Lifting and Handling Protocols:
Clear guidelines on manual handling techniques, including posture, load assessment, and when to request assistance or mechanical aid. - Use of Lifting Equipment:
Step-by-step procedures for operating cranes, forklifts, reach stackers, and other machinery, including pre-operation checklists and lockout/tagout rules. - Container Stacking and Securing:
Safe stacking heights, locking mechanisms, and tie-down procedures to prevent shifting or tipping during storage and transit. - Maintenance and Inspection Schedules:
Regular maintenance of equipment and containers to identify wear, corrosion, hydraulic leaks, or other faults that could compromise safety. - Emergency Response Protocols:
Clear instructions for responding to accidents, including first aid, spill control, evacuation plans, and incident reporting procedures.
Communication and Training
For safety procedures to be effective, they must be:
- Documented in accessible, easy-to-understand formats
- Communicated clearly to all employees, including temporary or part-time staff
- Reinforced through mandatory onboarding and refresher training sessions
- Visualized with signage, infographics, and floor markings in work zones
Regular safety drills and scenario-based training enhance preparedness and build confidence in workers, ensuring they can respond quickly and correctly in high-pressure situations.
Inspections and Continuous Improvement
Routine safety audits and inspections serve as a proactive measure to:
- Identify gaps in procedural adherence
- Monitor equipment condition and site readiness
- Evaluate training effectiveness
- Encourage feedback from frontline workers to refine processes
A well-structured safety management system is not static—it evolves through observation, incident analysis, and collaboration.
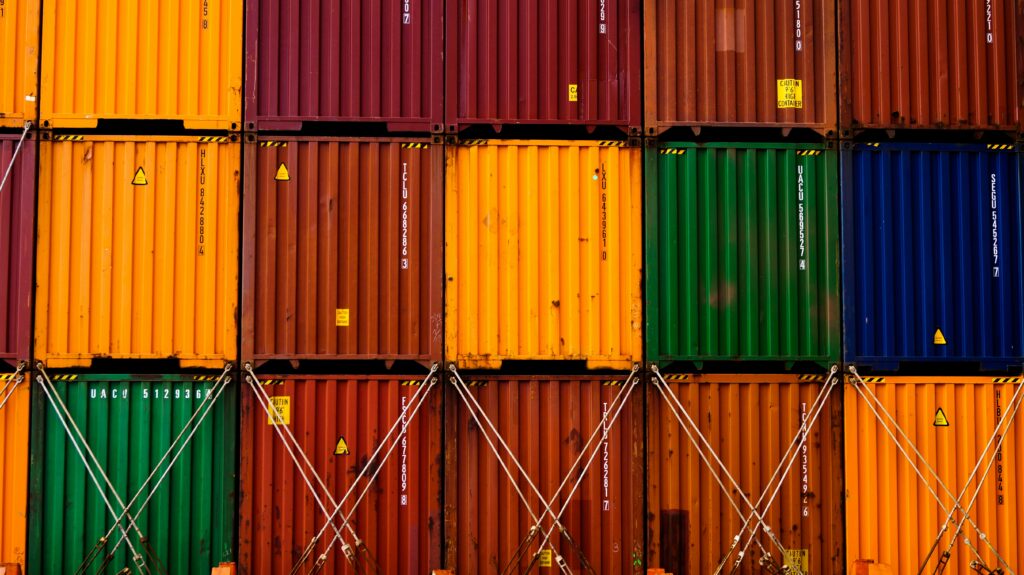
Handling Heavy Containers: A Mastered Art
The safe handling of heavy containers is not simply a skill—it is an art form forged through experience, discipline, and teamwork. It demands an ongoing commitment to:
- Learning and adapting to best practices
- Respecting the power of machinery
- Understanding the physics of weight and momentum
- Prioritizing safety above convenience or speed
Cultivating a Culture of Safety
Beyond individual compliance, safety becomes truly effective when it becomes a shared value across the organization. This means fostering a workplace culture where:
- Everyone feels empowered to speak up about hazards
- Supervisors lead by example
- Safety is integrated into daily operations, not treated as an afterthought
- Mistakes are seen as learning opportunities, not grounds for blame
A culture of safety is the foundation of operational excellence. When workers take ownership of their own well-being and look out for their colleagues, the risk of accidents decreases dramatically—and morale, productivity, and trust increase in turn.
In Summary
Mastering the safe handling of heavy containers is a journey, not a destination. It requires a lot of things:
- Well-defined procedures
- Proper tools and maintenance
- Regular training and communication
- A company-wide mindset rooted in responsibility and vigilance
By investing in safety and making it a core part of the organizational is identity, you not only prevent injuries and protect assets—you build a stronger, more resilient operation that can thrive under pressure.
Because in the end, the true art of the container handling lies not in muscle or machinery, but in the mindset of safety.
Conclusion
In conclusion, mastering the art of moving heavy containers safely is a skill that requires knowledge, practice, and the right tools. It’s not just about physical strength, but also about strategy and technique. From the tips and tricks shared in this article, it’s clear that prevention is the best way to avoid injuries. Using the right equipment, like dollies and hand trucks, not only makes the job easier but also reduces the risk of injuries. Moreover, understanding and using the correct lifting techniques is paramount. These not only include the basic ‘lift with your legs, not your back’ but also encourage keeping the load close to your body and turning with your feet, not your torso. Furthermore, proper planning, communication, and teamwork can significantly enhance safety and efficiency. It’s also important to remember that rushing can lead to mistakes, so patience is key. Lastly, wearing the right personal protective equipment can provide an extra level of safety. By implementing these tips and tricks, anyone can master the art of moving heavy containers safely, making the process more manageable and reducing the risk of potential injuries.